Sketcher Best Practices
Overview: As you may have experienced, successfully constraining sketches can sometimes be an art form. The key is
to place the dimensions and geometric constraints in such a way that they adequately capture your design intent. Most likely, you will
develop your own set of best practices as you gain experience with the Sketcher workbench. In the meantime, below you will find some
suggestions that make constraining sketches easier.
General Suggestions
In general, geometric constraints control the shape, orientation, and function of sketch curves. For this reason, it is a good
modeling practice to apply geometric constraints first. This step is especially true for horizontal and vertical geometry, or parallel and
perpendicular geometry. For instance, angles are sometimes created when lines are not parallel, rather than the desired distance dimension.
In this case, proper tangency positioning is important, because arcs will not stay aligned without the constraint present.
The second step is to add dimensional constraints after you add the base geometric constraints. Dimensional constraints help control the size
and location of the sketched profile. Designers add dimensional constraints in various ways; it usually comes down to personal preference.
Some individuals start with angular and radial dimensions, and then create length and offset dimensions, others move around constraining
important areas first, while others add constraints in a clockwise or counterclockwise progression.
As you add dimensions, pay attention to the way remaining geometry reacts when you change a value. Fix missing geometric constraints as
necessary. For example, if you see that a line changes from its horizontal position, repair it before attempting to add a dimension relative
to it.
Inferred Constraints
Automatically creating geometric and dimensional constraints can be helpful, but be careful of unnecessary constraints, particularly
coincident constraints, which can lock arc centers in position or constrain two lines in a collinear alignment. Looking for the dotted lines
of a coincident constraint at a distance can help you to resolve many over-constrained and conflicting constraint situations.
Remember, you can press SHIFT to suppress automatic constraints temporarily and you can use the SmartPick tool to help create the profile.
Testing Sketches
Use Select to drag under-constrained elements in the Graphics window to interrogate the profile for the open degrees of freedom.
Remember, an element in green may not be fully constrained. You can also determine how the rest of the profile will react given the current
constraints.
Sketch Analysis, another tool to consider using, determines whether extraneous geometry exists in the sketch, and if the sketch is closed.
See Sketch Operations, Sketch Analysis for more detail on Sketch Analysis.
Drawn Profile Size Versus Real Size
Several Options exist that you let you adjust your initial sketch when it is too big or too small. You can:
1. Redraw the profile (a time intensive solution).
2. Use Select to move the elements closer to their final position (a good solution only when some elements are incorrectly scaled).
3. Scale the entire profile (great solution if your entire profile is out of scale). Sometimes it is also helpful to create all the
dimensional constraints before going back and editing them to their final size. See Transformation for more detail.
Pay attention to the Sketch Tools toolbar when creating the first few elements in your sketch. Make sure those first elements are relatively
close, plus or minus 15% of the final size. You can decide the placement and size of the remaining elements based on these 'known' elements,
which becomes especially effective when the initial elements are some of the larger elements in the sketch.
Sketch Complexity
The 'keep it simple' rule definitely applies when creating sketch profiles. It is not necessary to add all the details to one sketch,
and you can use multiple sketches and solid features to create your final part. Using simple profiles in your sketch makes constraints easier
to use. To do so, you leverage the stable geometry in the first sketch to help constrain the later sketches.
Leave out unnecessary details that can be applied externally as solid features, such as sketch corners (fillets) and sketch chamfers. Add
sketch corners only when they help capture design intent, such as a tangent distance dimension relative to other geometry.
Construction Geometry
While keeping simplistic profiles can be helpful, we encourage you to use extra geometry to help constrain the sketch. For example,
if two arc centers are required to have a horizontal alignment, add a construction line between the two center points to constrain them. This
horizontal constraint on the construction line keeps the arc centers vertically constrained.
Remember, you can create points along a curve you can use when dimensioning and constraining. You can also constrain other curves to these
points for location control.
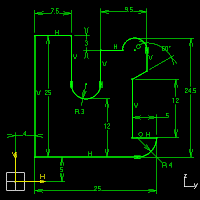
See Full-Size Image
Overview: As you may have experienced, successfully constraining sketches can sometimes be an art form. The key is
to place the dimensions and geometric constraints in such a way that they adequately capture your design intent. Most likely, you will
develop your own set of best practices as you gain experience with the Sketcher workbench. In the meantime, below you will find some
suggestions that make constraining sketches easier.
General Suggestions
In general, geometric constraints control the shape, orientation, and function of sketch curves. For this reason, it is a good
modeling practice to apply geometric constraints first. This step is especially true for horizontal and vertical geometry, or parallel and
perpendicular geometry. For instance, angles are sometimes created when lines are not parallel, rather than the desired distance dimension.
In this case, proper tangency positioning is important, because arcs will not stay aligned without the constraint present.
The second step is to add dimensional constraints after you add the base geometric constraints. Dimensional constraints help control the size
and location of the sketched profile. Designers add dimensional constraints in various ways; it usually comes down to personal preference.
Some individuals start with angular and radial dimensions, and then create length and offset dimensions, others move around constraining
important areas first, while others add constraints in a clockwise or counterclockwise progression.
As you add dimensions, pay attention to the way remaining geometry reacts when you change a value. Fix missing geometric constraints as
necessary. For example, if you see that a line changes from its horizontal position, repair it before attempting to add a dimension relative
to it.
Inferred Constraints
Automatically creating geometric and dimensional constraints can be helpful, but be careful of unnecessary constraints, particularly
coincident constraints, which can lock arc centers in position or constrain two lines in a collinear alignment. Looking for the dotted lines
of a coincident constraint at a distance can help you to resolve many over-constrained and conflicting constraint situations.
Remember, you can press SHIFT to suppress automatic constraints temporarily and you can use the SmartPick tool to help create the profile.
Testing Sketches
Use Select to drag under-constrained elements in the Graphics window to interrogate the profile for the open degrees of freedom.
Remember, an element in green may not be fully constrained. You can also determine how the rest of the profile will react given the current
constraints.
Sketch Analysis, another tool to consider using, determines whether extraneous geometry exists in the sketch, and if the sketch is closed.
See Sketch Operations, Sketch Analysis for more detail on Sketch Analysis.
Drawn Profile Size Versus Real Size
Several Options exist that you let you adjust your initial sketch when it is too big or too small. You can:
1. Redraw the profile (a time intensive solution).
2. Use Select to move the elements closer to their final position (a good solution only when some elements are incorrectly scaled).
3. Scale the entire profile (great solution if your entire profile is out of scale). Sometimes it is also helpful to create all the
dimensional constraints before going back and editing them to their final size. See Transformation for more detail.
Pay attention to the Sketch Tools toolbar when creating the first few elements in your sketch. Make sure those first elements are relatively
close, plus or minus 15% of the final size. You can decide the placement and size of the remaining elements based on these 'known' elements,
which becomes especially effective when the initial elements are some of the larger elements in the sketch.
Sketch Complexity
The 'keep it simple' rule definitely applies when creating sketch profiles. It is not necessary to add all the details to one sketch,
and you can use multiple sketches and solid features to create your final part. Using simple profiles in your sketch makes constraints easier
to use. To do so, you leverage the stable geometry in the first sketch to help constrain the later sketches.
Leave out unnecessary details that can be applied externally as solid features, such as sketch corners (fillets) and sketch chamfers. Add
sketch corners only when they help capture design intent, such as a tangent distance dimension relative to other geometry.
Construction Geometry
While keeping simplistic profiles can be helpful, we encourage you to use extra geometry to help constrain the sketch. For example,
if two arc centers are required to have a horizontal alignment, add a construction line between the two center points to constrain them. This
horizontal constraint on the construction line keeps the arc centers vertically constrained.
Remember, you can create points along a curve you can use when dimensioning and constraining. You can also constrain other curves to these
points for location control.
No comments:
Post a Comment